FCT COMBUSTION NEWSLETTER: October 2023
Dear Friends,
I hope this newsletter finds you happy and healthy as we enter the final quarter of 2024.
It is no secret that over the past 5 years, FCT has invested significantly in research and development to bring cleaner combustion solutions to the market. It is our mission to assist our partners in reducing – or completely negating – emissions from their combustion processes.
We have introduced various new technologies, or improved upon the capabilities of existing ones, to ensure our partners have access to the best available solutions to improve quality, safety, and productivity, while also ensuring this can be done in a mindful and environmentally responsible way.
We are encouraged by the feedback we are receiving from our customers, and the trust they continue to place in us. It has been pleasing to see the adoption of our technologies and the successful delivery of large scope projects for our clients in various countries around the world.
Some highlights during this time have included the safe and successful commissioning of iron ore pelletizing burners capable of firing hydrogen for multiple plants, and we are currently designing and supplying a hydrogen fired calciner (50-70 MW) for an alumina refinery in Australia. We are pleased to be at the forefront of hydrogen-suitable design for combustion processes across the world.
It has also been pleasing to see the cement industry’s increasing interest in Green Cement in recent years. FCT was an early mover in the development of flash calcining and rotary kiln calcining technologies for green cement production. Our specialist team, who have more than 40 years of experience in working with calcined clays, have also developed a novel solution to control the traditional cement ‘grey’ hue with an inorganic modifier. This solution is considered superior to others available in the market due to the absence of hazardous emissions, lower CO2 emissions, and lower heat consumption.
It is an exciting time for FCT, and it is a joy to see the company continue to grow in terms of our product range, the size of our projects, and the strength of our team.
I hope that you will enjoy reading our latest newsletter, and please do not hesitate to contact our team anytime if we can be of help. You can contact us via our contact page or follow us on LinkedIn
Wishing you all the best,
Adriano Greco
FCT Group CEO
PROJECTS ACROSS THE GLOBE
RECENTLY COMPLETED OR CURRENTLY ACTIVE PROJECTS ACROSS FCT COMBUSTION INCLUDE:
AUSTRALIA: Rio Tinto, Yarwun
FCT has been awarded the contract to design and supply the burners, H2 and O2 valve trains and burner management system for Rio Tinto’s 50-70MW hydrogen fired calciner at the Yarwun alumina refinery in Gladstone, Queensland. Hydrogen will replace natural gas eliminating CO2 emissions from the combustion process. This is an important step in Rio Tinto’s path towards decarbonising alumina refining. Australia is the world’s largest producer of bauxite and the largest exporter of alumina.
AUSTRALIA: BHP Olympic Dam
FCT is commissioning an oxy-fuel burner package for BHP’s flash smelting furnace at Olympic Dam in South Australia. The upgrade will extend the life of the furnace. In addition to the custom burners for both the North and East walls of the Settler Bath, accompanying burner management systems, valve trains, oxygen analysers and ancillaries are also included within the scope.
AUSTRALIA: Albermarle, Kemerton
FCT has been awarded the contract to deliver the burners, valve trains, gas analysers, and burner management systems for Lines 3 and 4 of Metso’s lithium pyro-plant in Kemerton, Western Australia. The project follows the successful delivery of Lines 1 and 2 at the same plant, with the commissioning of Line 1 already complete.
BRAZIL: Undisclosed client
FCT has been awarded the contract to supply a new vertical hot gas generator in Brazil. The supply comprises the complete 52 MW hot gas generator including the burner, fuel oil valve train, fuel oil pumping and heating skids, igniter system and the components to safely operate the system. The new HGG will combust fuel oil and coal to generate hot gases at controlled temperatures to supply thermal energy to a rotary dryer.
BRAZIL: Vale, São Luiz
FCT has been awarded the contract to supply 36 burners to Vale’s iron ore pelletizing plant in São Luiz, Maranhão. The scope also included valve trains, flow meters and various other equipment to convert the kiln to natural gas and improve operational safety.
BRAZIL: Vale, Vitoria
FCT has delivered 196 burners to Vale’s iron ore pelletizing plant in Vitoria. The scope also included valve trains, flame sensors, igniters, gas analysers, flow meters and various other equipment to convert the kilns to natural gas and improve operational safety. Commissioning of 44 burners and equipment for Kiln 3 was completed in June, with commissioning of burners and equipment for subsequent kilns to follow in the next months as scheduled in accordance with planned stoppage and availability.
Burners and valve trains being manufactured for Vale in Brazil
BRAZIL: Icon Máquinas, Criciuma
FCT has been awarded the contract to supply 3 new hot gas generators to Icon Máquinas in Criciuma, for which the final customer is Vale’s New Steel project. Two of the natural gas fired Hot Gas Generators will be installed in the Vitoria plant, and the third Multi-Fuel equipment will be installed in Vargem Grande, MG. All Hot Gas Generators will be supplied in partnership with Icon, who will integrate the equipment to their dryers.
CANADA: Undisclosed client
FCT has been has delivered a new hot gas generator to an undisclosed customer in Canada. The supply comprises the complete hot gas generator including the burner, valve train, igniter system and the components to safely operate the system. The new HGG will combust natural gas to generate hot gases at controlled temperatures to supply thermal energy to a rotary dryer. Commissioning is planned to happen in the next months.
FCT has delivered a hot gas generator to a client in Canada
CAMEROON: Undisclosed client
FCT has delivered a complete fuel oil system for a calciner and a hot gas generator, from truck unloading pumps to valve trains inlet. The scope includes tanks, filtering, pumping and heating stations. Commissioning is expected to take place towards the end of 2023.
EUROPE: Undisclosed Country/ Client
FCT has been awarded a contract as part of a Pellet Plant Refurbishment Project to supply 38 combustion systems and peripheral equipment and services for natural gas, coke oven gas, and the ability to be converted to hydrogen in the future. The main goals of the project are to have new combustion systems with a large turndown ratio on all fuels, allowing safe and smooth operation from the beginning of kiln preheating up to full production, while controlling NOx emissions. The scope of supply includes burners, burner blocks, igniters, flame sensors, fuel valves and safety equipment, combustion air fans with distribution manifolds, and a CFD study. The equipment has been delivered, and commissioning is scheduled for the second half of 2023.
FRANCE: HeidelbergCement, Bussac Foret
FCT has been awarded a contract by DAL Engineering Group to deliver a Turbu-Flex™ burner for HeidelbergCement’s Bussac Foret plant. The targets of the project are to maximise the use of alternative fuels as well as to improve combustion control. Commissioning recently took place in August 2023.
INDIA: Birla Corporation
FCT has delivered Birla Corporation with a calciner for firing petcoke and coal.
NAURU: Republic of Nauru Phosphate Corporation (RONPHOS)
RONPHOS has two rotary dryers for drying phosphate rock, each with its own hot gas generator. FCT has delivered a combustion system including one oil burner, a primary air fan, an oil pumping skid, an oil valve train, and Burner Management System. The combustion system is designed to utilise both waste oil and diesel. Commissioning is expected for the next months.
TAIWAN: IHC Mining/ Chemours, Kuan Yin
FCT is supplying a combustion system for IHC Mining’s Recovered Ore (RO) Dryer at Chemours Kuan Yin Rutile (TiO2) plant.
USA: Undisclosed client
FCT has recently commissioned a complete combustion system for one of the largest clinker lines in the USA. The pyro-processing line uses natural gas as the main fuel. The scope supplied and commissioned by FCT included:
- Gyro-Therm™ burner with trolley, gas valve train, and burner management system (BMS)
- 4 x calciner burners with associated valve trains
- 2 x Hot Gas Generators for cement mills, including BMS and other accessories
USA: Texas Lime Co., Cleburne
FCT has been awarded a contract to supply a new dual-fuel Gyro-Therm™ burner for the Cleburne plant in Texas. The new main burner can fire up to 100% coal and 100% natural gas. The supply includes the accessories and add-on to the burner, as well as igniter, flame sensors, fans, and burner trolley.
USA: Ash Grove Cement, Leamington
FCT has commissioned a set of K-Jet Calciner burners and a warm-up burner for Ash Grove’s Leamington plant in Utah. The burners will improve the mixing and heat distribution when operating with natural gas. To complete this engineered solution, a dedicated safety gas valve train for the safe start up, control and shut down of natural gas was included in the scope, as well as a new Calciner BMS system.
PEOPLE OF FCT
At FCT, we know that our continued success is largely due to our team’s commitment to providing the best products, service, and expertise across all our offices. We are pleased to announce the newest additions and changes within our team:
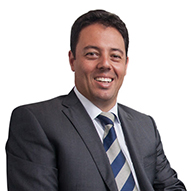
Rodrigo Elisei, Chief Operating Officer, FCT Group
We are delighted to announce Rodrigo Elisei has accepted the position of COO across the FCT Group of companies. A high performing operations-management executive with more than 20 years of experience, Rodrigo brings a wealth of expertise to the role managing operations across all of FCT’s business units worldwide.
Previously, Rodrigo held the role of Global Business Development Executive at FCT Combustion, focusing on the Iron and Steel industries. Prior to this, Rodrigo worked at Vale for many years at all pellet plants of the Brazilian conglomerate. During this time, Rodrigo held roles such as Executive Operations Manager of 3 plants as well as Chief Operating Officer of Vale Oman overseeing all operational functions including HSE, maintenance, production, process, planning, quality, and laboratory.
A graduate of the renowned Federal University of Ouro Petro in Brazil, Rodrigo also holds an Executive International Master of Business Administration.
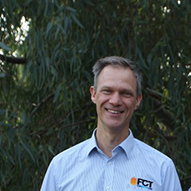
Roger Hassold, CEO (Asia-Pacific)
We are pleased to announce Roger Hassold as the CEO of FCT Combustion (Asia-Pacific). With more than 30 years of experience working with combustion, including roles in Technical Management, Sales Management, Production Management, and Process Engineering, Roger brings a wealth of technical and commercial experience to the role.
Roger has been part of FCT for almost 10 years and, prior to this, worked at Adelaide Brighton Cement (ADBRI) for more than 20 years. Roger graduated from the University of Adelaide with a Bachelor of Chemical Engineering (degree with Honours), as well as the Consortium Advanced Management Program Certificate.
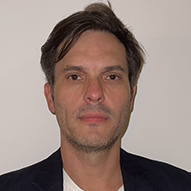
Renato Greco, Internal Technical Advisor
We are delighted to announce that Renato Greco has joined FCT Combustion in the role of Internal Technical Advisor, helping to lead the development of new technologies with a focus on reducing environmental impact for our clients in their pyro-processing lines.
Renato has been involved in key projects with FCT in the design of novelty equipment for the iron ore pelletizing and clay calcination processes, and has previously held positions such as CEO at Greco Combustion Systems and Director of New Technologies at ENFIL Environmental. He brings a vast amount of experience in designing the entire pyro-processing lines for various industries, including environmental technologies to reduce CO2, SOx, VOCs, particulates, among others. Renato also has a deep understanding of Computational Fluid Dynamics (CFD).
Having graduated from the University of São Paulo with a degree in Chemical Engineering, Renato went on to complete a Master of Business Economics at Fundação Getúlio Vargas. He is also a graduate of the Stanford University Executive Program, and holds an International Certificate in Corporate Finance from Colombia Business School. Renato is fluent in Portuguese, English, Spanish, Italian, and French.
CONFERENCES & EVENTS
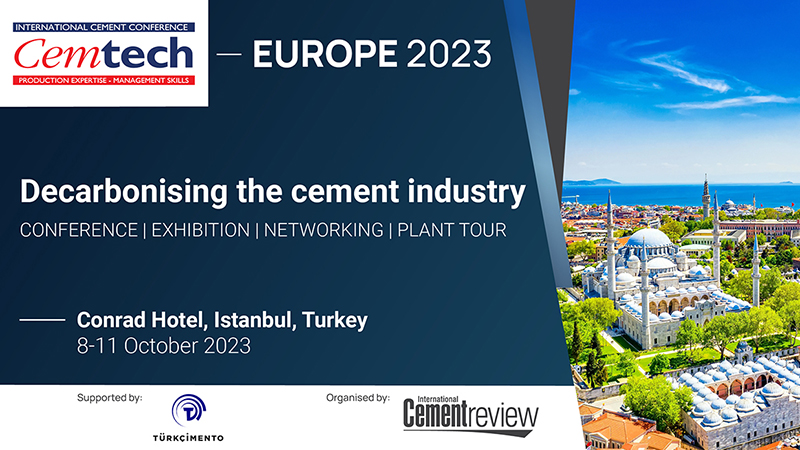
Joel Maia will be a Presenter at Cemtech Europe, being held in Istanbul from October 8-11. Meet us at Booth #17!
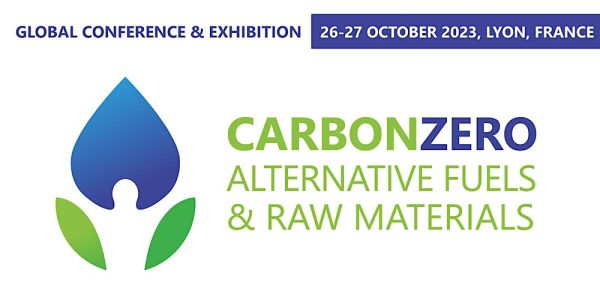
Joel Maia will speak on the subject of ‘Decarbonizing the cement industry: Calcined Clays and Alternative Fuels’ at the Carbon Zero conference being held in Lyon, France from October 26-27
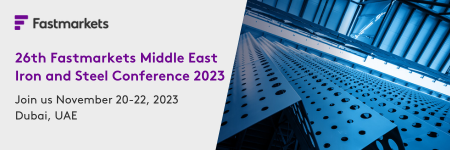
FCT is proud to be a sponsor of the 26th Fastmarkets Middle East Iron & Steel Conference in Dubai, held from November 20-22. Adriano Greco, Rodrigo Elisei, Michael Zhu, and Adilson Nico will attend. Please join us at Booth 1&2
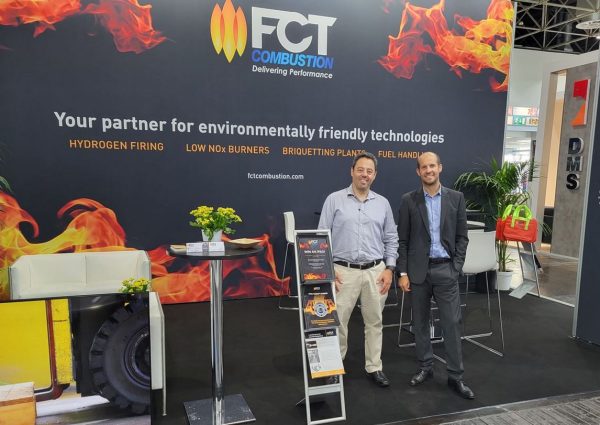
FCT was pleased to attend the METEC trade fair in Dusseldorf, Germany. It was wonderful to meet so many industry colleagues!
Joel Maia presented “Maximizing alternative fuel usage while minimizing CO2 emissions” at the Cemtech webinar ‘Getting the most from alternative fuels’, which was held in July.
Clay Calcining Pilot Plants
FCT Combustion offers two clay calcining technologies for the production of Green Cement: FlashCalx flash calciner and RotaCalx rotary kiln calciner. In the video, you can see the test rigs we use to test our client’s material before they move to the industrial size installation. The test rigs are fully operational and colour control devices are in installation. Our specialist team have more than 4 decades of experience in clay calcining and are ready to help you. For more information about clay calcining, including presentations and downloadable materials, please click here
FCT ACTech and FLSmidth sign agreement
Cement plants have a new solution for online analysis of raw materials thanks to a partnership between FLSmidth and FCT ACTech. Part of the FCT Group, FCT ACTech delivers complete, end-to-end analytical solutions for the cement, mining and mineral processing industries. The new agreement will see FLSmidth incorporate FCT ACTech’s analyser units into their new QCX CUBE analysis solutions for the cement industry.
“We are very pleased to be able to integrate FCT ACTech analyser units in our new QCX® CUBE analysis solutions for cement plants,” commented Jens Asbjørn Pedersen, Global Product Manager for Sampling, Preparation and Analysis. “We are starting with the launch of QCX CUBE X10, which primarily targets raw meal applications, but it is our ambition to utilise FCT ACTech’s innovative range of analyser units to also deliver advanced online XRD analysis solutions for clinker and cement.”
Offering plug-and play functionality, the QCX CUBE X10 is designed for seamless integration with FLSmidth’s market-leading QCX/BlendExpert™ optimisation software. This allows the speed and frequency of online analysis to be combined with the precision analysis provided by an automated sampling system and well-performing central laboratory to establish very tight chemical quality control of the raw meal mix.
FCT ACTech’s innovative instruments for process control allow customers to improve their profitability and reduce their carbon footprint. A variety of analysers are available in the range, including the FLX Free Lime Analyser, the RMX Raw Meal Analyser, and the OFX Elemental Analyser with Free Lime Channel, among others. To find out more about the range, please click here or to learn more about the agreement, please click here

Our European Headquarters has moved to a new location
FCT Combustion (Europe) has recently moved to a larger office in Vienna, Austria! The move will better accommodate our growing team, which has been driven by an increased number of projects within the European & African regions.
FCT has offices located in Australia, Austria, Brazil, China, and the USA, as well as agents around the globe. To contact your local team, please click here
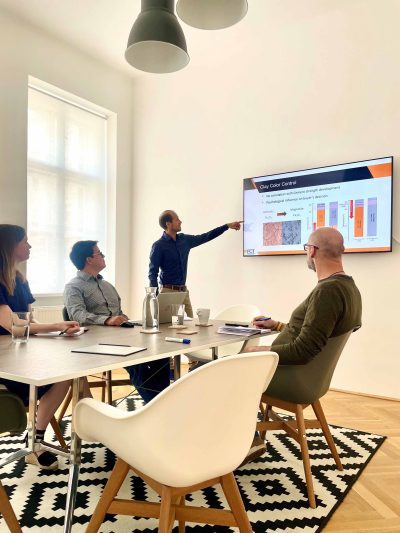
Burner Q&A
In the June edition of World Cement, FCT participated in a burner Q&A session. Download the article here, or keep reading below to learn more about optimal burner design for different fuel types, emissions reduction, improved performance, and increased productivity.
CO2 and NOx are the main emissions of concern in the cement industry, but these emissions can be significantly reduced by utilising a specialist burner.
Calcination of limestone is the main cause of the CO2 emissions in cement production, followed by combustion products, while NOx emissions are caused both as an inherent by-product of the combustion process and due to heat flux characteristics.
Regarding the CO2 emissions there is not much a burner can do, except increase its efficiency, which would reduce the CO2 emissions from the combustion, or replacing the fuels for some with less or no carbon, such as hydrogen for instance. To reduce the CO2 emissions from the limestone calcination, a complete shift in technology is required, such as the replacement of clinker by calcined clays.
The kiln burner design can influence NOx emissions significantly because NOx is correlated to several factors under the burner control, such as: flame ignition distance from the front of the burner, total primary air volumes, axial air and swirl air distribution and location, rate of secondary air entrainment, flame momentum, among others.
A burner which can control heat flux also has the ability to control NOx. FCT’s innovative Turbu-Flex™ burner has been designed to meet this challenge and includes a nozzle that can be adjusted to suit the fuel mix by offering two modes to operators: one mode is characterised by a more moderate flame specifically for reducing NOx emissions, while the other maximises Alternative Fuel firing and thereby reduces CO2 emissions.
FCT’s Turbu-FlexTM burner allows for two operating modes against emissions by the pressing of a button in the control room: the boost mode, designed for efficient combustion of high rates of alternative fuel and the standard mode, for NOx reduction.
When speaking specifically about gaseous fuels, FCT’s patented Gyro-Therm™ burner was designed with these factors in mind, and uses precessing jet technology to significantly reduce NOx. Clients have reported a reduction of more than 30% in their NOx emissions, compared to the use of traditional turbulent jet burners.
Some of other harmful emissions can also be reduced by a proper combustion control by the main burner. A short and intense flame will for instance help to reduce SOx emissions trapping the sulphur inside the clinker matrix instead of being thrown in the atmosphere with the exhaust gases. Other minor components can benefit from similar effect.
A distinction has to be made between firing alternative fuels at the calciner and at the rotary kiln.
To ensure efficient combustion in the calciner, it is important to study the aerodynamics to ensure RDF is introduced in the correct location to experience full residence time, oxygen availability, temperature zones and mixing, as these are the major aspects impacting an efficient combustion. In many cases, FCT has used Computational Fluid Dynamics (CFD) to modify tertiary air inlet ducting, goose neck, exit ducting and firing locations to improve aerodynamics, turbulence and temperature distribution, improving combustion performance and raw meal calcination.
In the rotary kiln burner, RDF can be successfully fired at high substitution rates above 80%. Depending on the characteristics of the RDF to be used, it can be introduced via a channel in the burner, or it can be introduced adjacent to the burner in a satellite burner. The knowledge accumulated over the years with difficult to burn fuels shows that flame momentum, secondary air entrainment, injection location and distribution of fuels and air within the flame, together with the characteristics of the alternative fuel itself, are the major influencing points on an efficient combustion at high substitution rates.
In cases where high substitution rates are difficult to achieve, a study, which may include a CFD part can help understand the reasons why and find the solutions to allow high rates.
Hydrogen is an emerging fuel which could replace traditional fossil fuels when it is able to be produced from renewable energy in sufficient quantities and at a reasonable cost.
At present, small amounts of hydrogen can be introduced in the kiln burner, where it can have positive effects on early ignition of alternative fuels. Any hydrogen usage will reduce CO2 emissions from the combustion process as well as allow the use of more alternative fuels.
FCT’s current range of multi-fuel burners can be adapted for hydrogen in rotary kilns, and we have previous experience successfully installing burners with hydrogen substitution of up to 65% in other high temperature processing industries.
FCT is a key partner of the Heavy Industry Low-carbon Technology (HILT) CRC research program, which includes a focus on hydrogen, and works alongside academic and industry partners to find solutions for the challenges that currently exist in mainstream hydrogen adoption, including potential for lower heat transfer to the clinker as well as the potential for NOx emissions to increase due to the high adiabatic flame temperature.
FCT is concurrently developing a rotary kiln burner design capable of firing up to 100% hydrogen. Our R&D team has already designed a Low NOx iron ore pelletizing version of the burner for traveling grate kilns, which is in the prototype phase and will be tested in the facilities of an industry partner in Europe in 2023.
An article which explores hydrogen as a method for reducing CO2 emissions in clinker production in greater detail, including its productions, benefits and downfalls was written by FCT, and is available is available to read here. We recommend this for further reading and better insight on this topic.
Burner design plays a very important role in process stability. The burner produces the flame and radiation which is used in the clinkering process. The flame length and radiation profile are critical to controlling the burning zone temperature and location. A stable burning zone location and temperature leads to stable kiln operation.
To counteract the natural variations of the process, a burner with flexible operation is required. In that way, the burner can cope and even minimize some instabilities caused by factors other than the burner itself such as fuel characteristics, raw material variability, operational instabilities, among others.
FCT’s Turbu-Flex™ burner has large operational range, specifically designed to be able to adjust to the needs of the client. The burner can be operated in Standard mode or Alternative Fuel Boost Mode, depending on the operator’s choice of fuel, and features one ‘on-off valve’ to easily switch between the two with no interruption to operation or production.
As fuel mixes change, particularly if using variable RDF, it is important the burner maintains a stable flame length and position. In some specific cases or for troubleshooting, FCT uses CFD to ensure the burner is matched to the kiln aerodynamics and range of expected fuel mixes to ensure a stable burning zone.
Monitoring parameters in the burner, such as the primary air and gas pressures and flows (if gas is used as a fuel), are essential to ensuring the burner is in good mechanical condition. Any deviation outside normal operating conditions should be investigated immediately to minimise damage to a burner. Additionally, the temperature at some critical burner parts can be online measured to anticipate any failure.
Intentional burner design also reduces maintenance costs and increases lifetime. FCT considers the expansion of burner channels relative to each other in its design to avoid damage from differential expansion. Tip designs do not constrain axial expansion.
FCT also uses special coatings on critical face plate items to prolong burner life, as well as using wear-resistant materials, high grade heat resistant steels, smart design to minimise wear and facilitate maintenance.
As Hydrogen becomes more prevalent, it will deliver environmental benefits with CO2 reduction. However, it is important to note that the use of hydrogen will create its own challenges from its combustion properties, as it burns with low radiation and high NOx. Additional considerations will include bespoke valve train design to deal with Hydrogen leakage, component selection due to Hydrogen embrittlement issues, Burner Management System (BMS) design and safety due to the very wide flammability limits, and flame detection due to the low radiation. FCT is experienced in working with hydrogen and can assist operators in safely adopting the new fuel into their process.
Alternative Fuels (AF) including Refuse Derived Fuels (RDF) will also continue to shape burner design. In particular, the use of biomasses will likely be popular for their low-to-no nett CO2 emission appeal. For high levels of AF and RDF fuel substitution in the rotary kiln, FCT offers the Turbu-Flex™ burner, which is proven and trusted by clients across the globe. For the calciner, a well-designed injection point will contribute to higher substitutions.
FCT has a team of in-house CFD Specialists who can assist clients in optimizing the design for their specific needs. CFD gives insights that cannot normally be seen, and can assist in solving “new” and challenging problems that are yet to appear.