DOWNLOAD AS PDF:
FCT COMBUSTION NEWSLETTER: NOV 2017
FCT COMBUSTION NEWSLETTER: NOV 2017
Download as PDF: Newsletter Masterclass
Dear FCT community,
FCT Combustion continues to develop and grow and make its mark in all corners of the globe.
In addition to our main base in Australia, we now have successful business units operating in the US and Middle East. Our European and Brazilian subsidiaries are developing strongly, enabling us to reach and service more customers globally.
While our burner related business is predominantly in iron ore pellet kilns, cement kilns and lime kilns, there is a spread across other mineral processing industries as well. Our research and development is leading to improved burner designs and combustion modeling tools for the benefit of customers with better efficiency, increased, flexibility and lower emissions.
As we continue to grow globally, one of the challenges we face is keeping our customers and associates informed about our new technologies and project wins. Through this new newsletter, we aim to keep you regularly informed about developments at FCT.
I trust you find the newsletter useful – enjoy the read!
Managing Director
FCT International
ASH GROVE CEMENT AND THE VALUE OF
LONG TERM RELATIONSHIPS
In October of this year, agreement was reached for the international building material group CRH plc to proceed with the US$3.5 billion acquisition of Ash Grove Cement Company. The transaction is expected to be completed by the end of 2017, so it seems fitting to now look back on our history with Ash Grove.
At the heart of Ash Grove’s corporate culture is the fostering of long standing relationships, and FCT has been a part of this with the companies’ relationship spanning more than two decades. This has provided FCT with an opportunity to demonstrate the breadth and depth of our exceptional capabilities in combustion technology.
Ash Grove is the largest American owned cement producer and has always been highly motivated to ensure their own competitiveness and sustainability. Ash Grove’s mission has been to play a key role in the World Business Council for Sustainable Development and the Cement Sustainability Initiative. FCT has supported Ashgrove to deliver on this commitment to environmental stewardship and social responsibility through our CFD modeling, design and supply of state of the art kiln burners and the expertise of our process engineers.
FCT Combustion began working with Ash Grove in 1996. Our first installation was a Gyro-Therm burner at the Durkee, Oregon plant and the resulting fuel savings, production increases and reductions in NOx were stunning, significantly improving upon this plant’s previous performance.
Since then, FCT has modelled many of Ashgrove’s cement kiln and calciner combustion systems and/or supplied burners for kilns in various Ash Grove locations: Leamington, Utah; Inkom, Idaho; Louisville, Nebraska; Montana City, Montana; Chanute, Kansas; Seattle, Washington; and Midlothian, Texas.. As the preferred vendor for burner systems, FCT has delivered the expertise to add value to Ashgrove’s bottom line and to assist them to meet ambitious operational goals.
This year FCT completed projects for Ash Grove at their Midlothian and Seattle plants that again produced strong results. In particular, for the Midlothian cement plant we designed, supplied and installed a Gyro-Therm burner, replacing a less than satisfactory coal and gas burner. The Gyro-Therm burner again proved a slam dunk, giving a step change improvement in the operation of the Midliothian kiln.
Ash Grove’s Process Engineers showed great enthusiasm to get the Gyro-Therm running, which was evidenced with the cold commissioning being completed in advance of FCT’s engineer arriving in early May. Tasked with the design and commissioning of the burner, the FCT Senior Process Engineer, stepped off the flight to Dallas late in the evening, proceeding directly to the plant to get started on the hot commissioning.
The Midlothian’s Gyro-Therm has a 196.6 MM Btu/h (57 MW) firing rate capacity. In the first few weeks while the kiln was stabilizing, the Gyro-Therm burner demonstrated significant improvements: compared with the previous burner, fuel consumption dropped, ammonia usage (and therefore NOx emissions) decreased and, qualitative results indicated an increase in production, improved burning zone coating stability and the removal of the need for oxygen injection. The clinker quality also reported an improvement, which was evident by the microscopic images taken.
The belief that Ash Grove has placed in FCT Combustion has been well rewarded. We look forward to continuing this relationship for many decades to come.
PROJECTS ACROSS THE GLOBE
RECENTLY COMPLETED OR CURRENTLY ACTIVE PROJECTS ACROSS FCT COMBUSTION INCLUDE:
Europe
Industria Cementi Giovanni Rossi, Piacenza, Italy. Burner upgrade: Implementation of segmentally variable primary air in an industrial kiln burner. The main target is improvement of current RDF firing rate of 80% through modifications in the burner tip and body, increasing momentum and changing air distribution in the flame.
Cimenteries CBR – Heidelberg Cement Group, Antoing, Belgium. Burner upgrade: Main targets are the improvement of operational safety when using oxygen, improvement of burner performance with alternative fuel rate above 70%, increasing momentum and improving the operation with liquid fuels through a new lance and nozzles.
Americas
Lehigh (Heidelberg), Evansville, Pennsylvania. Two low NOx Gyro-Therm MKII burners: The supply includes the burners, BMS, valve trains, pilots, trolleys, flame scanners and primary air fans. The burners will be fueled by petcoke, natural gas and RDF.
Lehigh (Heidelberg), Leeds, Alabama. Calciner burning system including valve train.
Loesche GmbH, for CSN Arcos, Brazil. Two Turbu-Jet AF burners including oil lances, LPG electric igniter and primary air blowers with VFD.
Mountain Cement – Eagle Materials, Laramie, Wyoming. Installation of two flame monitoring systems.
Graymont, Eden, Wisconsin. CFD modeling and engineering for gas conversion of two low NOx Gyro-Therm MKII burners for the plant. The burners will fire petcoke and natural gas.
Graymont, Cricket Mountain, Utah. Pre-heating burner system.
Ash Grove, Midlothian, Texas. Gyro-Therm MKII burner.
Ash Grove, Seattle, Washington. Gyro-Therm MKII burner.
Ash Grove, Leamington, Utah. CFD study for the kiln and calciner.
Ash Grove, Durkee, Oregon. Calciner burner and natural gas valve train.
CRH, Mississauga, Ontario, Canada. Calciner burner pre-heating system with pilot and flame monitors.
Asia-Pacific
Cement Industries of Malaysia Berhad (CIMA), Malaysia. Turbu-Jet AF burner with primary air blower and trolley assessment for Kiln Line No. 2 (Perlis Plant).
SinoSteel Equipment and Engineering Company, Algeria. Iron ore pellet burners, with gas valve trains and burner management systems despatched for installation in Algerian iron-ore pelletizing kiln.
Siam Cellulose Wangsala, Thailand. Turbu-Jet AF burner successfully commissioned on biogas in lime kiln, as part of pulp mill.
Vale, Oman. CFD modeling of iron-ore pelletizing kiln burner.
Cement Australia, Australia. Assistance in the planning, management and execution of the return to service process for the Gladstone cement kiln shutdown.
Boral Cement, Australia. Gyro-Therm burner light-up review.
Australian Paper Mill, Australia. Process engineering assistance with HAZOP and SIL assignment, in preparation for lime kiln upgrade.
PEOPLE OF FCT
Asia-Pacific
Dr Jordan Parham is now CEO of FCT Combustion Pty Ltd (Asia-Pacific) and is based at our headquarters in Adelaide, Australia. Jordan was previously Engineering Manager at FCT Combustion.
Roger Hassold is now Sales Manager Asia Pacific. He joined us as a Process Engineer in 2014.
Tim Marriage has joined FCT as Engineering Manager. He comes to us from Minelab Electronics, where he was the Mechanical Engineering Domain Lead. Previous to this, Tim was Engineering Manager at Thermo Fisher Scientific.
Renata Favalli joined FCT in June this year. She is currently based in Brazil and is working on projects across FCT, in conjunction with the Adelaide office. Her exceptional talents as a CFD Modeler were previously utilized by Dynamis Mechanica Aplicada Ltda and IPEN.
Americas
Ilker Demircan has joined FCT Combustion. He comes to us from cement industry leaders, Cemex USA, bringing a wealth of understanding from the client side of combustion, and Pimentos, Turkey, where he was Process Manager.
Alex Polmo joins FCT as a Project Manager with a strong background in combustion. His most recent roles included Capital Project Manager at Cabot Corporation and Senior Project Engineer at Flare Industries for their Latin America region.
CONFERENCE HIGHLIGHTS
AND UPCOMING EVENTS
Asia-Pacific
Roger Hassold, Sales Manager Asia-Pacific will represent FCT at the 25th ASEAN Federation of Cement Manufacturers Technical Symposium & Exhibition in Bandung, Indonesia in April 2018. He will be presenting on ‘Maximizing Alternate Fuels using modeling and flexible burner design’. To book a time or enquire, click here.
Roger Hassold also represented FCT at the TCMA (Thai Cement Manufacturers Association) Conference in Thailand. FCT’s Thai agent, Chaiphat Thanasupakorn also staffed the booth, enabling us to give visitors an excellent introduction to our products and services. Our stand was specifically sought out by several industry members on the recommendation of their colleagues. This desire to know more about FCT’s capabilities was borne out by Roger being asked to give an impromptu presentation during a dinner pre-conference and the repeated requests for him to give a full presentation on burners.
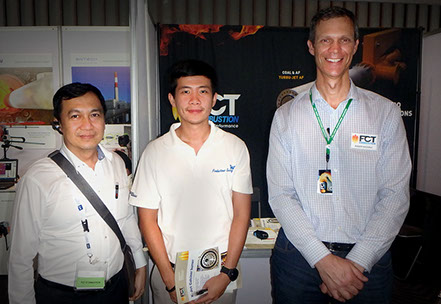
FCT agent Chaiphat Thanasupakorn (L) and FCT’s Roger Hassold (R) with a visitor to the booth
This year we have had several waves of university students conducting valuable work placement experience within FCT. We liaised with all three major universities in Adelaide to secure over 20 students from engineering, marketing, business and international studies. Highlights have been their work on analysis of Saudi Arabia’s cement industry for Combustion, market analysis of Cement World articles on combustion companies across the world, assisting FCT Flames with their marketing strategy and the River Torrens Project. International students have also been translating the FCT website, brochures and marketing material.
Europe
Joel Maia, Technical Director of FCT GmbH in Germany presented at the Global CemFuels Conference in Barcelona, Spain in February on ‘Calciner case study: Experience and advanced tools for fuel and production optimization’.
Joel also presented at Cemtech Rome 2017 in early October, speaking on ‘An alternative fuels program: the model approach’. He followed this up by representing FCT in the CETA booth at TCMB Antalya, Turkey.
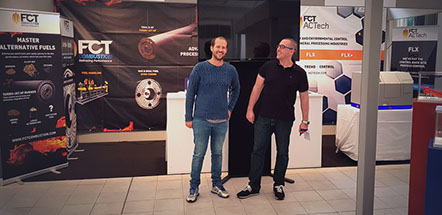
FCT’s Joel Maia (L) and Bogdan Iancu (R) at the Cemtec Conference in Rome
Americas
FCT will be presenting at INTERCEM Americas 2017 in Las Vegas in November. We look forward to meeting with our customers and associates there. To book a time or enquire, click here.
Adriano Greco presented at the 2017 TAPPI PEERS Conference in Norfolk, Virginia in November on ‘Successful conversion to gas firing – How to get the best outcome for productivity and emissions’.
FCT Combustion exhibited at Tappi KilnCon 2017 in Savannah, Georgia in August.
FCT took Calgary Cement Conference by storm in May. With around 600 supplier booths at the 2017 IEEE-IAS/PCA Cement Industry Technical Conference held in May, we’re proud to report FCT’s booth was one of the best attended and received. Our booth was constantly busy and the business we generated at the Calgary conference makes it one of our most successful ever.
FCT presented at the XXXIV FICEM Technical Conference 2017 in Guatemala in September on ‘Safe Conversion to Natural Gas for Lime Sludge Kilns’. We also showcased our capabilities with an exhibition booth.
MASTERCLASS:
FUELS, FLAMES AND RADIATION
What are we trying to achieve when firing fuel in a rotary kiln? Simple really, we want to heat the product to the desired temperature with as much of the heat going to the product and as little as possible leaving with the flue gas, whilst minimizing the generation of NOx. There are three modes of heat transfer: Radiation, Convection and Conduction. The most significant of these in a high temperature rotary kiln is radiation, accounting for 95% of the heat transferred with the remainder transferred via convection
We can simplify the situation if we say the energy from combustion (EComb) heats the products of combustion, raising the sensible heat of the combustion gases (ESens) and radiating heat from the combustion gases in the flame to the product and bricks (ERad). This can be expressed as follows:
Whilst the equation above looks complex, it is important to understand it as a number of conclusions can be drawn from it.
1. The maximum flame temperature occurs when the ERad term is zero meaning that all the combustion energy goes into heating the gaseous products of combustion.
2. This is referred to as the adiabatic flame temperature. The adiabatic flame temperature for a number of fuels is shown here in Table 1. As you can see, fuels with higher Carbon: Hydrogen ratios tend to also have higher flame temperatures.
3. The maximum flame temperature also occurs when there is just the right amount of air for combustion, ie. there is no excess air (excess air coefficient is 1). If the flue gas products mass flow, ṁ, is increased by increasing the excess air co-efficient above 1, then the flame temperature is reduced as some of the energy from combustion is going into heating the additional air. If ṁ is reduced, such that the excess air coefficient is less than 1 and there is insufficient air for complete combustion, then the amount of energy released will be reduced, resulting in a lower flame temperature also. The effect of excess air on the adiabatic flame temperature for methane combustion in air is shown here in Figure 1. Due to less than perfect mixing in the real world, a small amount of excess air, say 10%, is required to ensure that complete combustion is achieved and the heat available to the product maximized.
4. Preheating of the fuel and air for combustion, T1, also contributes to increasing the flame temperature. Given the quantity of air required for complete combustion is in the order of 9-10 times the quantity of fuel, preheating of the combustion air results in a much larger increase in flame temperature than preheating of fuel. The impact on flame temperature from preheating combustion air is shown here in Figure 2.
5. To maximize radiant heat transfer the difference in the flame and product temperature,
must also be maximized. Put another way, the temperature of the product surface exposed to the flame, Tp, must be minimized. Therefore it is important that the product cascades rather than slides to ensure product from the core of the charge is brought to the surface and in contact with the bricks. As can be seen in Figure 2, the product takes up less than half the kiln circumference meaning that the bricks receive more of the direct radiation from the flame than the product. As a result the product receives more heat by conduction in contact with the bricks than by direct radiation from the flame. Therefore cooling of the bricks as they pass under the cascading product is important to help maximize heat transfer to the brick and in turn to the product.
6. The area, A, for heat transfer is also important. This applies to both the area of product exposed to the radiant flame and the volume or size of the radiant flame itself. Kiln speed, refractory /coating surface condition, and stickiness of product play a part in the area of the bed exposed to the flame as it climbs up the side of the kiln and cascades back down again. Also a wide, short flame near the tip of the burner will concentrate the heat transfer at the discharge end of the kiln, while a longer narrower flame will distribute the heat further into the kiln.
7. The flame emmissivity, ε, also plays an important part. Increasing the emissivity of the flame can dramatically improve radiant heat transfer to the product and in turn reduce the flame temperature. One benefit of the reduced temperature for flames with high emissivity is lower thermal NOx emissions. To demonstrate this, consider a flame in a rotary kiln heating clinker to 1450°C. If we start with a luminous flame with Tf1=1750°C and ε 1=0.95 and then compare that to a non-luminous flame with ε 2=0.3 we see the non-luminous flame would need a temperature of:
In other words, the non-luminous flame temperature is about 2140 – 1750 = 390°C higher than the luminous flame. This calculation is clearly over simplified but stands to show how flame emissivity affects the flame temperature.
Different fuels result in flames with different flame emissivities. A rough guide to flame emissivities for different fuels is:
Coal ε > 0.95
Oil ε = 0.7 – 0.9
Gas ε = 0.3 – 0.6
In the next Masterclass we’ll explore practical methods for reducing NOx in rotary kiln flames.
View all newsletters: